Main Spar Construction
We will use a moldless construction technique to build the main spar; all we
need is a relatively flat surface such as a garage floor. We
will start with a 24” X 96” sheet of 4.5 lb. last-a-foam
and cut two long strips, bonding them end-to-end. This will
become the foam core of our spar. We will install phenolic
hard points where the spar mounts to the fuselage and again where
the outboard spars attach. The primarily shearweb will be laid
up over both sides of this foam core. At this point we will measure
out lengths of our graphlite carbon fiber and bond them together
to form our spar caps. Foam will be removed from the top and
bottom edges of the spar as was done in the fabrication of the outboard
spars and we will install the primary spar caps.
We will then bond the lengths of carbon fiber graphlite to form
the four secondary sparcaps. Two each will be mounted on top
of the spar and two each will be mounted on the bottom of the spar. Finally
we will layup the secondary shearweb over these caps creating a monolithic
spar assembly.
Let us get started.
Cut a 96” length of ½” last-a-foam 13” wide. Make
sure the edges are dead straight. Make a diagonal cut lengthwise
6” on one side 7” on the other.
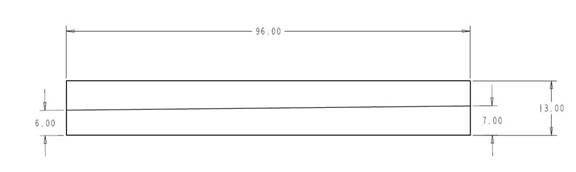
Rectangular ½” Last-a-Foam Stock
Place the 7” edges together other and tip the ends upwards. Use
a laser level to draw a line between top corners of the outside tips
and drop the center 3.5” for dihedral. See the drawing below.
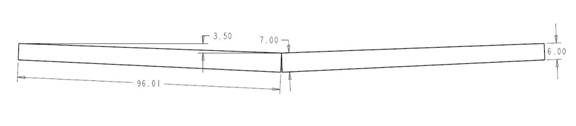
Put smaller ends together and tip up ends for dihedral
Next, trim the two pieces at the center to mate cleanly. Micro the
joint. Measure 21” outward from center to each side. Now we
need to create a smooth, curved transition between the two sides
of the spar. This transition is created by removing a little
material from the bottom center section of the spar, and adding a
little material to the top middle section. See the following
photo. Remove .33” from bottom center and smooth to blend at
21” on each side. Add foam to the top edge between 21” to
21” on each side rising .41” in center and also blend
into a smooth curve.
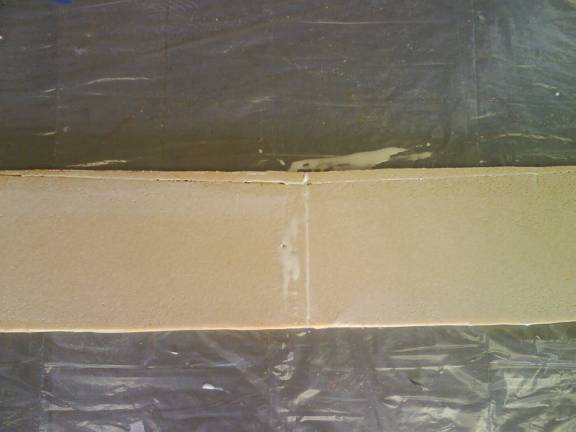
Center Spar Joint – material added on top, removed from bottom
Cut six squares of ½” thick phenolic. Measure outward
from the center of the spar and center the blocks up and down and
at the points measuring 17.5”, 76.25”, 93.875” from
the center. The outboard hole is about 2” from
outside edge. Rough up the phenolic blocks with coarse
sandpaper as you did with the outboard spar blocks and install them
with thick micro.
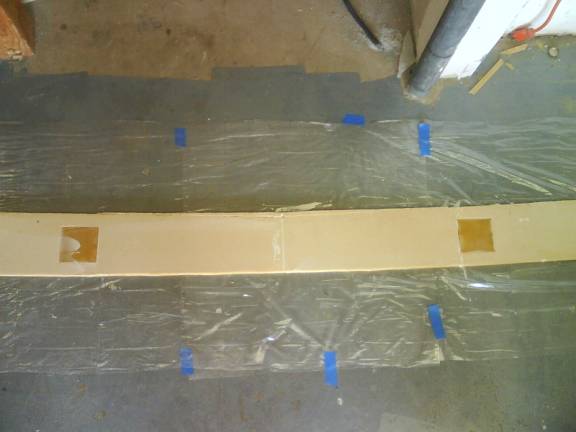
Center phenolic Blocks Installed
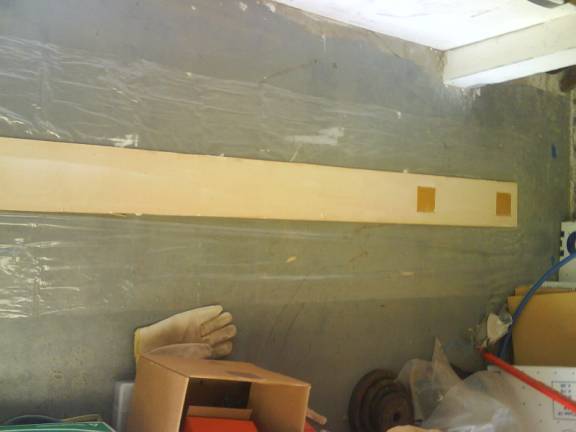
Outboard phenolic Blocks Installed
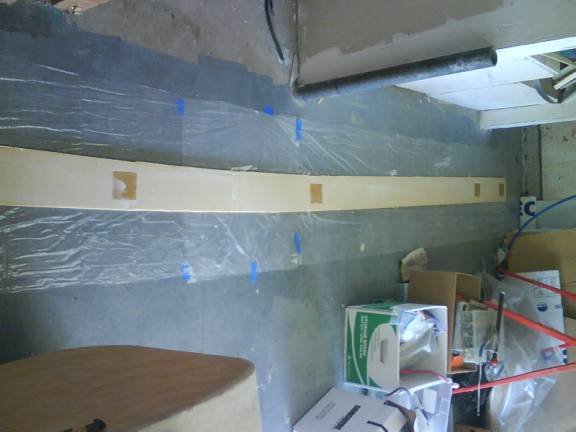
Ready to layup Primary Shearweb
We are now ready to install the primary shear webs. Mark the
spar front and back as each side has a different layup schedule.
On the front side of the spar mark 31 inches from the center on both
sides and 66 inches from the center on both sides. The front
of the spar will have five layers of BID fiberglass installed on
the 45 degree bias. The first layer will run from 31 inches
on one side to 31 inches on the other side. The second layer
will run from 66 inches on one side to 66 inches on the other side. Finally,
layup three additional layers over the entire length of the front
side of the spar. Refer to the following table for the layup
schedule for the primary shearweb.
Layer 1st
Front 1st Rear
1 31” 57”
2 66” entire
len.
3 entire
len. entire
len.
4 entire
len. entire
len.
5 entire
len.
Be sure to use a layer of peel ply over the final layup as we will
be adding a secondary shear web structure later.
Repeat this process on the back side of the spar using the Rear
layup schedule in the table above. The rear shearweb has only
4 layers of fiberglass BID.
Once the epoxy has cured, remove the peel ply and carefully trim
the front and rear shearwebs to the exact size of the foam. Clamp
a straight edge to the spar to insure a nice straight, clean trim
job.
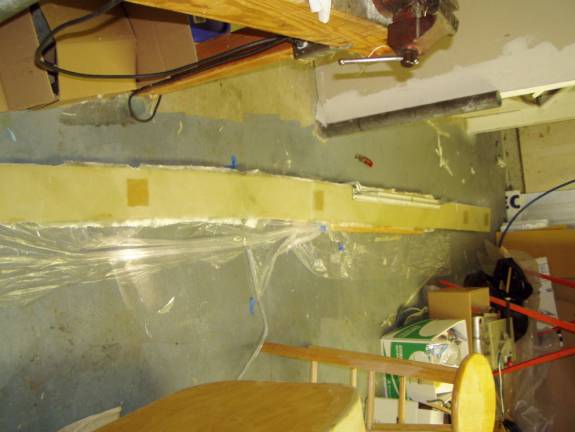
Trimming shearweb to match foam
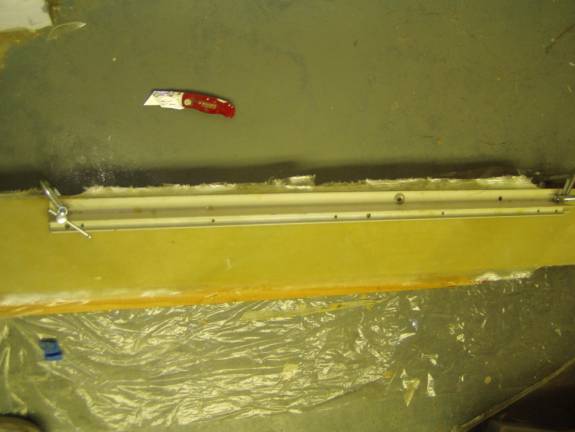
Trimming the primary shearweb to the foam edge
It is now time to fabricate the sparcaps. There will be primary
and secondary sparcaps. You can fabricate them all now or fabricate
them as needed. I prefer to fabricate all six caps at once. The
caps are refered to as: the primary top, primary bottom, secondary
front top, secondary rear top, secondary front bottom and secondary
rear bottom.
The spar caps are made from varying lengths of our carbon fiber
graphlite material. All of the sparcaps for the center wing
spar are symmetrical about their center point. That is, mark
the center of all of the individual lengths of graphlite and they
will line up to form the center of the completed, bonded spar cap.
Refer to the following table and cut the necessary lengths of graphlite
for the two primary spar caps. Each is composed of six lengths. Be
very careful when handling and preparing the sparcaps. The
graphlite material is easily cut with a pneumatic cutoff wheel and
should be sanded with 100 grit sandpaper and cleaned with acetone
before bonding. Use gloves and a respirator when performing
these tasks in a well ventilated space. I do this outdoors
dressed in protective gear. Be very careful when handling the
graphlite as tiny slivers of the material can come loose and create
splinters. Do not breathe carbon fiber dust, once in the lungs,
it never comes out.
The spar caps are made by bonding the six lengths together using
the bottom curved surface of the foam spar as a mold. The longest
is placed against the foam spar first, followed by progressively
smaller lengths. This way the natural springiness of the material
will hold the strips together while they cure. A thin film
of epoxy is used to bond them together. Use a sheet of plastic to
protect the spar while the sparcaps are curing. As mentioned
before, it is preferable to fabricate all six sparcaps at this time. Refer
to the table further down the page for the length of graphite used
in the secondary spar caps.
Make primary caps.
Length bott
cap top
cap
1 138 152
2 156 168
3 176 184
4 192 192
5 192 192
6 192 192
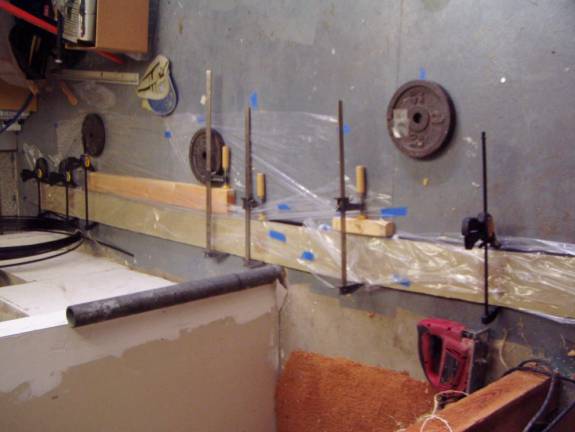
Using the spar as a mold for the sparcaps
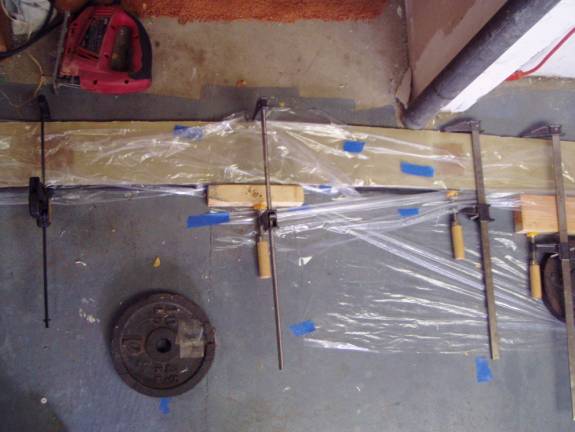
Using the spar as a mold for the sparcaps
Once the sparcaps are cured, sand them to remove excess epoxy residue
and create a rough surface for bonding to the spar. Again exercise
extreme caution to avoid carbon fiber dust.
Lay the top and bottom spar caps into approximate position and mark
the amount of foam that needs to be removed from the top and bottom
edges to bury the sparcaps. The spar caps should end up being
even or just below the trimmed shear web edges. Review the following
two photographs to get an idea of the desired pocket you want to
create.
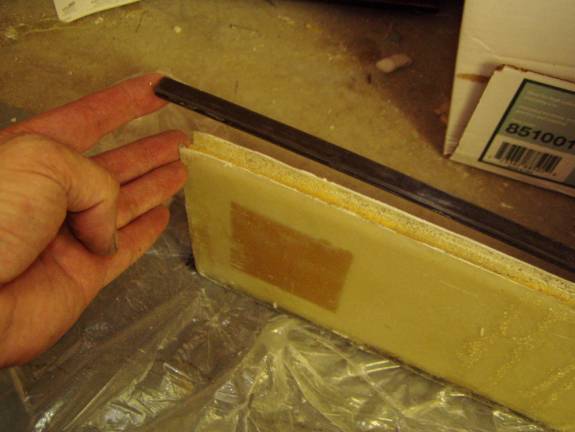
Foam removed for sparcap
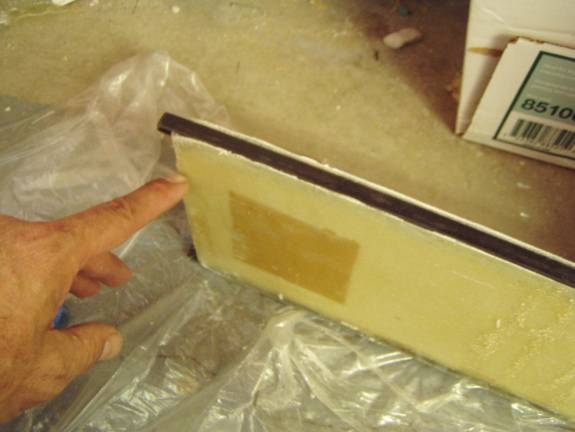
Test Fit Sparcap
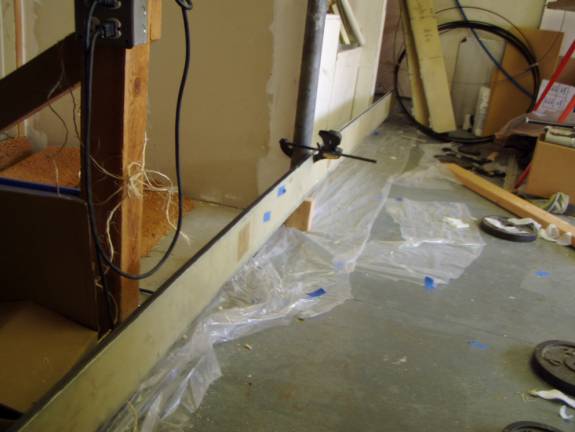
Sparcap ready to be bonded in place
Once you have removed just enough foam and test fit the spar cap
into the resulting pocked you are ready to bond it into place. Insure
that you do not mix the spar caps up. The top cap is thicker
than the bottom cap as Graphlite is slightly stronger in tension
than compression.
After building the outboard spars you are well prepared and understand
the techniques involved in installing the spar caps. We will
create a flox mixture and lay down a bead of it into the slot created
between the two shearwebs. We will then pour some epoxy resin
down on top of the flox and press the spar cap into place. The
flox mixture should ooze up the sides of the sparcaps and you need
to work out all of the air under the caps. Then clamp the sparcap
into position at or just below the edges of the shearweb. Clean up
as much overflow epoxy as you can, it is much easier to do it now
as opposed to waiting until after it has cured. Let cure.
Sand the top of the spar so the shearweb and sparcaps make a clean
transisiton. Trim the shearweb if required.
Now flip the spar over and install the bottom spar cap in the same
manner.
Congratulations you have completed the primary shearweb and primary
sparcap installations. Now we will move on to the secondary
caps and secondary shearweb fabrication.
Bond 48” length of ¼” last-a-foam to the
center section of the spar as shown in the following photos. Remove
the foam over the phenolic hardpoints and then trim the foam to a
bevel around the hardpoints. Trim the foam to match the shape of
the top and bottom of the spar. Refer to the following photos.
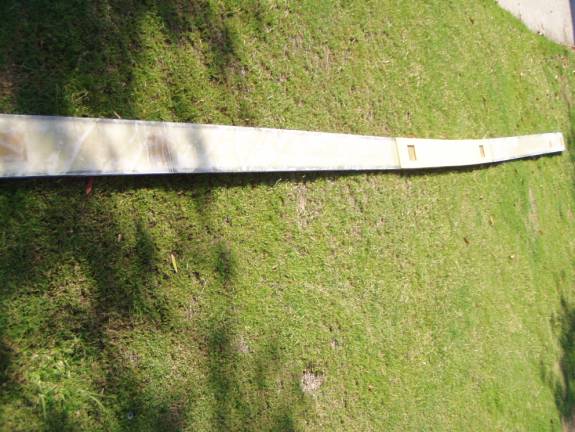
Primary sparcaps installed
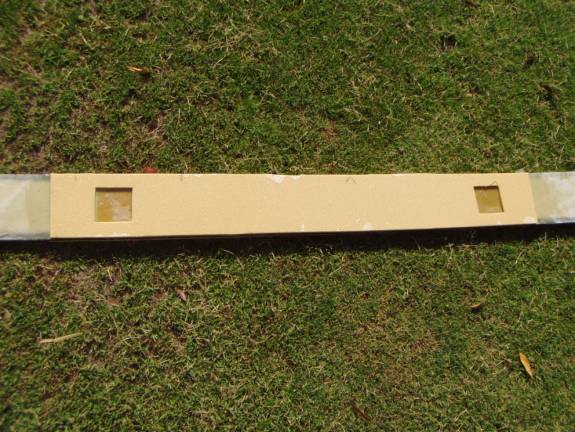
Center foam installed
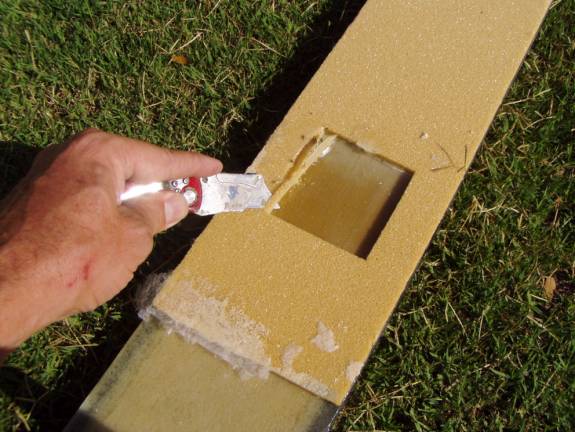
Bevel foam around phenolic hardpoints
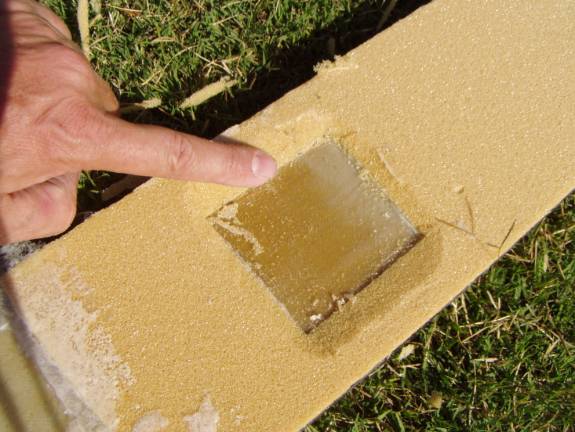
Bevel foam around phenolic hardpoints
The secondary sparcaps are installed next. The secondary sparcaps
are twice as wide as the primary sparcaps and are made from two sets
of bonded strips of Graphlite Carbon fiber. If you have not
fabricated your secondary spar caps yet, do so now. The spar
is still easily used as a mold to shape the four spar caps.
Top Front secondary spar cap is 140 inches long, Top Rear Secondary
sparcap is 126 inches in length, Bottom Front Secondary sparcap is
124 inches in length and the Bottom Rear Secondary spar cap is 108
inches in length. Use the following table to fabricate the
four secondary spar caps as was done with the primary sparcaps. Top
Front secondary spar cap is made from 5 strips of Graphlite, Top
Rear Secondary sparcap is made from 5 strips of Graphlite, Bottom
Front Secondary sparcap is made from 4 strips of Graphlite, and the
Bottom Rear Secondary spar cap is made from 3 strips of Graphlite. The
spar caps are symmetrical about their center as were the primary
sparcaps.
Make secondary caps
Top
primary |
front |
rear |
152 |
56 |
46 |
168 |
74 |
64 |
184 |
94 |
84 |
192 |
116 |
104 |
192 |
140 |
126 |
192 |
|
|
Bottom
138 |
48 |
58 |
156 |
70 |
82 |
176 |
94 |
108 |
192 |
124 |
|
192 |
|
|
192 |
|
|
Next we need to make a pocket for the secondary sparcaps. I
used strips of MDF clamped to the top and bottom of the spar measuring
1 inch wide and ½ inch tall. These were tightly wrapped
in plastic to act as a mold release.
The center section of the spar is already one inch wide and a smooth
transition to the sparcap pockets is easy. The outboard sections
of the spar is only 1/2 inch thick and we need to us a thick micro
to create a radius under the MDF strips so the secondary shearwebs
can make a smooth transition from the ½ inch thick spar to
the 1 inch thick secondary sparcaps. Review the following
photos.
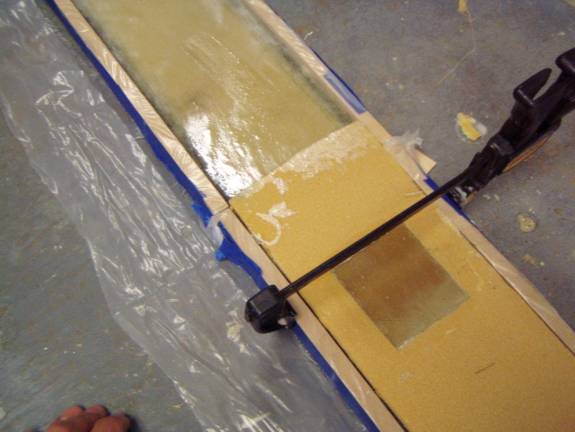
Clamp wood strips in place for sparcap pocket
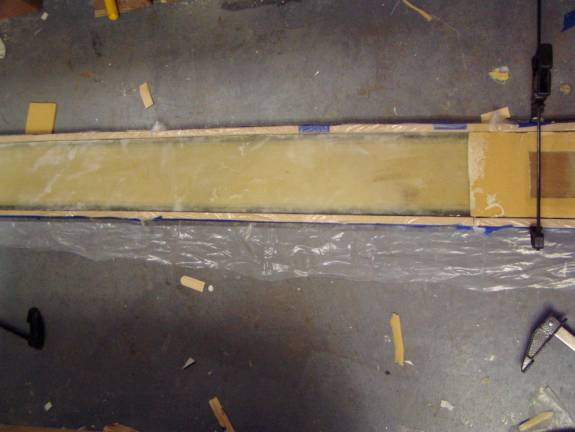
MDF Strips clamped to form sparcap pocket
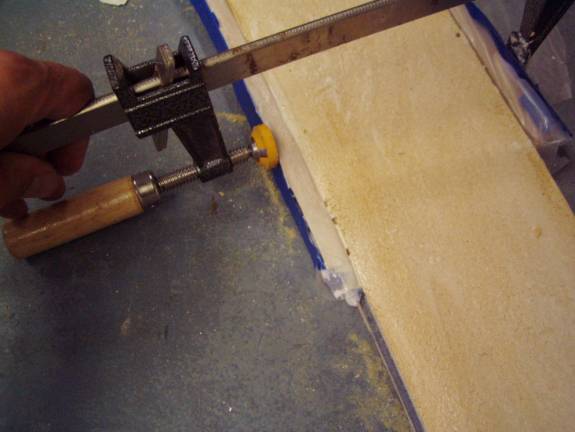
MDF Strips clamped to form sparcap pocket
Use two layers of BID to create the sparcap pockets. Refer
to the table above that defines the secondary spar cap lengths. No
need to make the sparcap pockets run the total length of the spar,
only put them where the spar caps need them. The fiberglass should
extend about an inch and a half onto the spar and cover the ½” deep
wooden strips. Once the fiberglass has cured trim the
edges to the height of the wooden strips and then remove them.
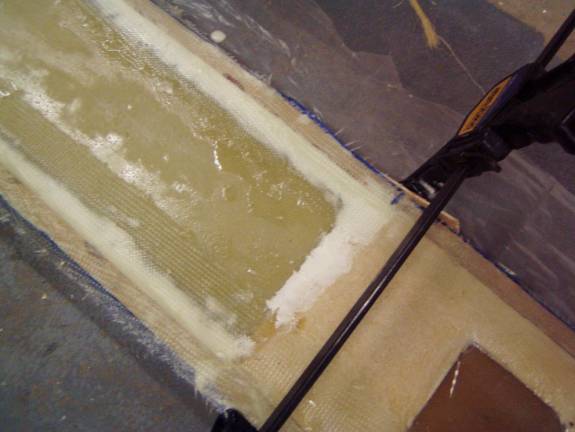
Micro radius
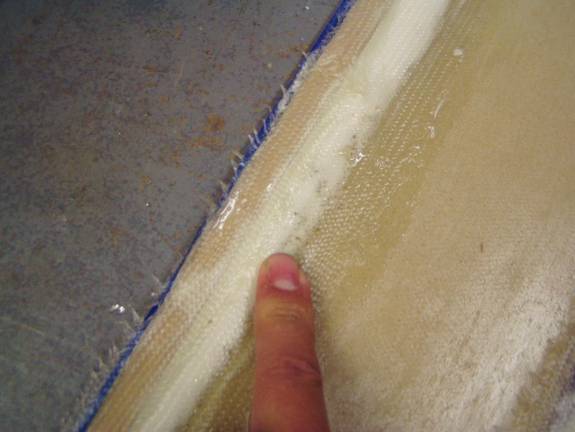
Another view of the Micro radius
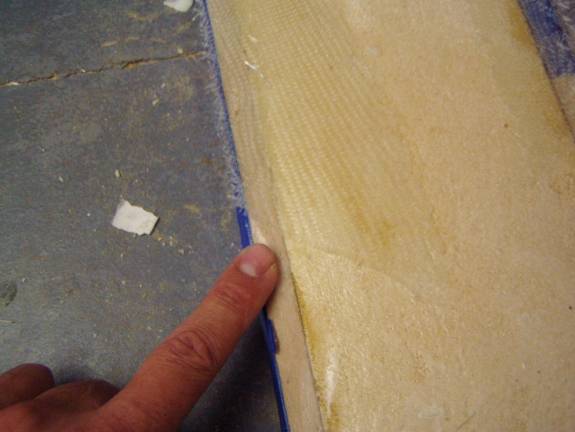
Pocket at mid spar
When you have formed your secondary sparcap pockets, test fit the
sparcaps. Remember to place them in the correct orientation,
there are four distinct sparcaps and each must be in the proper place.
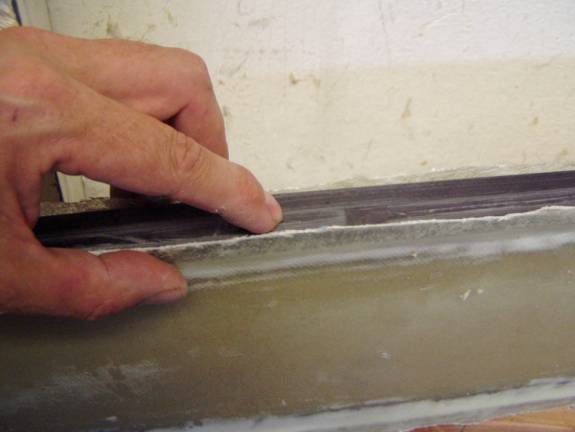
Test fit secondary sparcaps
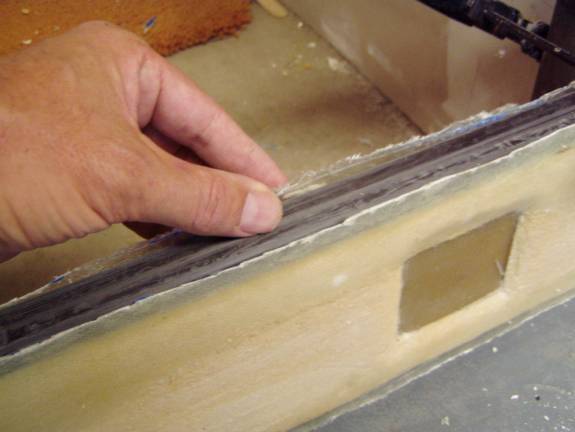
Test fit secondary spar caps
Once you are happy with the fit and orientation of the secondary
spar caps bond them in place as you did the primary spar caps. Use
plenty of epoxy and let it ooze out. This is no place to skimp
on resin. Clamp the sparcaps in place and let them cure.
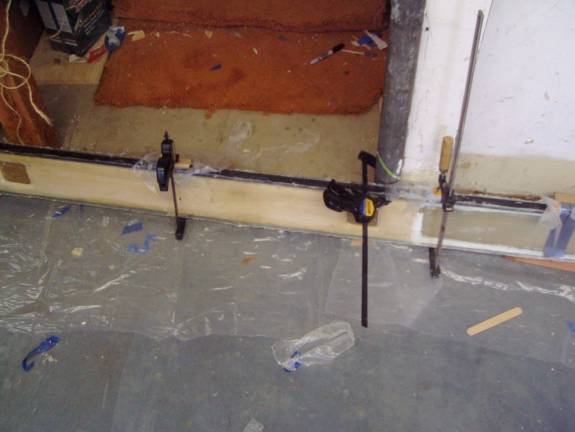
Secondary Sparcaps clamped in place
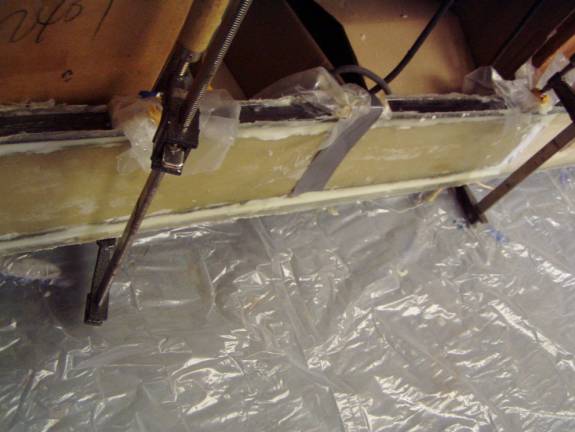
Secondary Sparcaps Curing
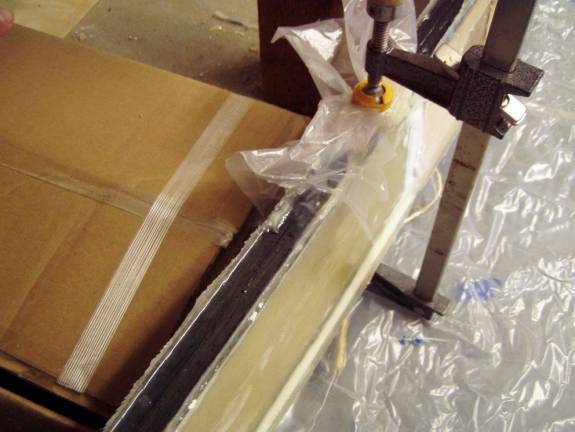
Note the Flox and Resin oozing between the sparcaps and shearweb
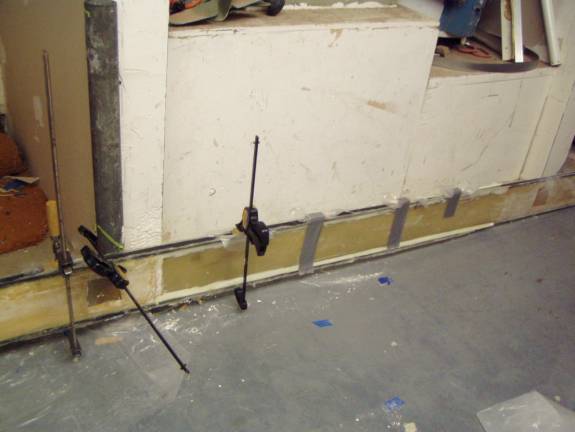
Clamps and duct tape secure spar cap during cure
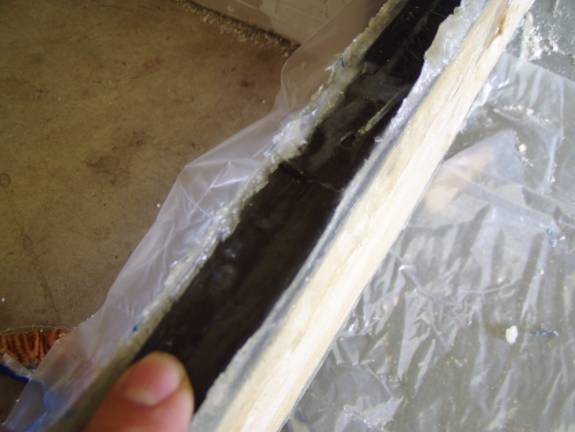
Note excess Flox and resin post cure
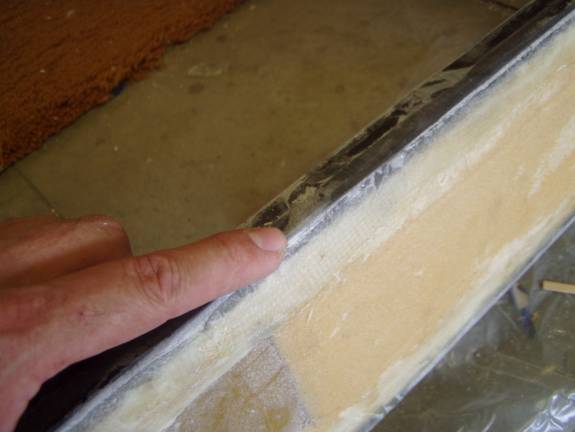
After cure, Sand down shearweb to top of sparcap
Once the sparcap is bonded in place, grind down any excess flox
and resin that may be standing proud of the sparcaps. Grind
the shearwebs and sparcap pocket to match the height of the sparcaps. Do
not grind into the graphlite
We now are going to seal the sparcap and create a nice radiused
top surface for the secondary shearwebs to bond to.
Mix up a batch of flox and epoxy resin and create a layer over the
sparcap. It does not need to be thick, only a 1/16 of an inch,
but it must cover the sparcap and fill in any transition points between
various graphlite rod pieces. See the next photo.
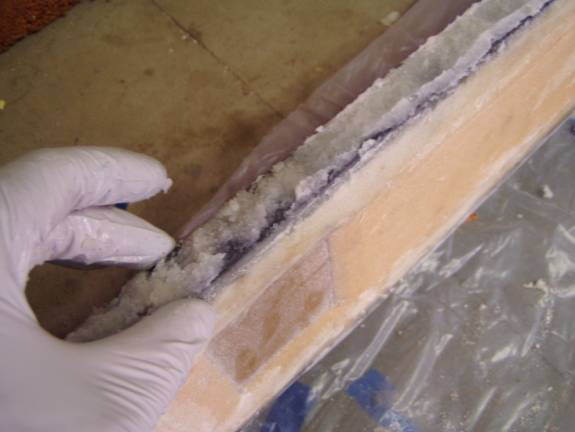
Flox spread over top of sparcap
Next layup a single BID layer over the Flox and smooth out all air
and create a nice radius. The BID should extend a couple of
inches down on each side of the spar as shown in the following photo. Use
excess resin in this step, then use paper towel to remove the excess. We
are striving for a nice smooth radiused top to the spar and absolutely
no air bubbles or voids in the sparcap structure. Work the
Flox out under the glass to create an even distribution side to side.
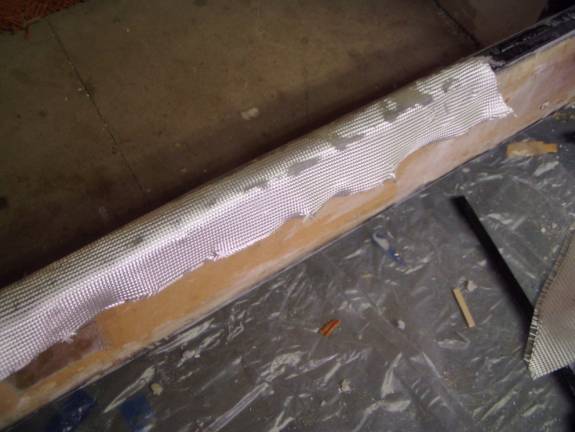
Fiberglass applied over the flox
The above picture shows a strip of fiberglass applied over the wet
flox. I found that a better approach to applying this BID was
to presaturate the cloth on a piece of plastic first. Wet the
sides of the spar with resin using a paint brush, then apply the
BID over the top of the spar. This way the fiberglass cloth
is wet out better.

The finished encapsulation of the sparcap
Notice in the above picture how even the flox is distributed under
the BID cloth and how there is a noticeable radius to the top of
the spar. This will make the application of the secondary shearweb
much easier.
Next add reinforcement strips over all of the phenolic hardpoints. The
four outboard hard points get two layers of BID, the first will be
4 inches wide and the second will be 5 inches wide. These will
extend beyond the sides of the phenolic and wrap around the top of
the spar. The spar is flipped over and the procedure is repeated
on the other side with the BID being wrapped around the bottom of
the spar and over the reienformcent on the other side. The
two inboard hardpoints get 4 reinforcement layers of BID, each 1
inch wider than the last and extending ½ inch further on
each side. These likewise wrap over and under the spar. This
helps transfer the forces from the shearweb to the spar caps.
Finally the secondary shearwebs are laid up. These are very
similar to the primary shearwebs with the exception that they overlap
the sparcaps. The shearweb is installed from the bottom of
the existing shear web, up the side, over the top and extending down
the other side about two inches. Then the spar is flipped over
and the other side’s shearweb is laid up, again from the bottom
of the existing shear web, up the side, over the top and extending
down the other side about two inches. This way the entire spar
is encapsulated in the BID creating the secondary shearweb.
The shearwebs are made up of 4 layers of BID, two partial length
layers and two full length layers. The first layer extends 50 inches
each side of the middle of the spar and the second layer extends
80 inches both sodes of the spar. Lay up the two partial length layers
first, cover the layup with peel ply and let cure.
A sparcap extension is added to the top of the spar. This
is fabricated from a strip of ½ inch last-a-foam. Below
is a drawing of the completed spar just to give an idea of the finished
product. The spar cap extension begins 19 inches from the center
of the spar, rises to its full height at 21 inches from the center
of the spar and then tapers to zero height at the spar tip. The
height of the extension at 21 inches from center is about 1.5 inches tall. Your height may vary but we are shooting for a spar height of just under 5.5" at the tip and 9 inches at the tallest point, 21 inches from the center.
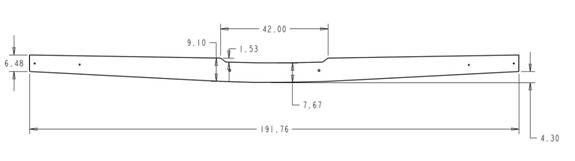
Once this extension is bonded to the top of the spar, micro is used
to fill in all empty spaces between it and the top spar caps.
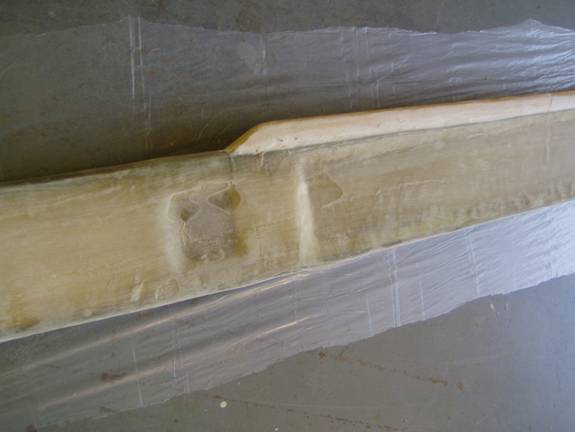
Finally,
two additional layers of BID are added to the shearweb on both sides of
the spar, wraping around the top and bottom as was done with the
two partial secondary shearweb layers.
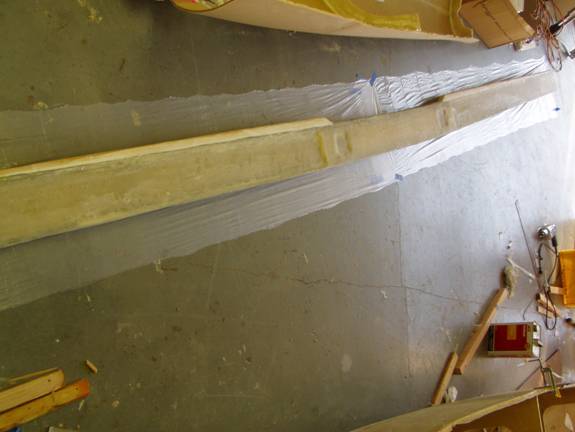
This completes the main spar construction. We still need to
orient and drill the mounting holes for both the outboard spar sections
and the fuselage mounting holes. We will do this next. Congratulations
on the completion of a major subassembly of the Super2.
PREVIOUS<---------------Manual
Home ------------------>NEXT |